Solar Farm Inspections
Pre-Construction Mapping and Digital Elevation Models for Optimisation
Monitor Construction Progress
Solar Farm Inspections
Infrared equipped UAVs alert operators to broken or non-functioning panels. Making sure these areas are fixed to maintain peak performance and output, helps avoid costly slowdowns or interruptions in service.
In the solar energy field, the usefulness of drones begins even before solar panels are installed. The thermal imagery and 3D mapping made possible with drones help inform the decision-making process on the optimal placement of solar panels for most efficient energy production. Once panels are installed and begin production, drones are crucial in providing information as to functionality. With their ability to quickly cover large areas, drones are absolutely essential in performing inspection of large solar arrays. Covering the same amount of ground on foot is painstakingly slow and inefficient. Thermal imaging is the key component here with the ability to alert operators to broken or non-functioning panels, as a solar panel with no or low output will be obviously cooler than the others. Making sure these areas are fixed to maintain peak performance and output, helps avoid costly slowdowns or interruptions in service.
Skyspec utilises Artificial Intelligence to generate reports that examine every aspect of you solar farm and any issues experiences are converted directly into loss of revenue estimates.
Available Levels of Inspection
Skyspec offers three levels of inspection; Overview, Standard, and Comprehensive. These levels differ in flight altitude, data capture time, level of analysis, and the level of detail in the final deliverables.
Overview Level Inspection
Summary: An Overview inspection is flown at the highest altitude, inspections are performed very quickly, due to a maximum flight speed, allowing for very large sites to be inspected quickly.
Infrared thermal imagery: 10-15 cm/px resolution
HD RGB Imagery: 5 cm/px resolution
Identifiable Anomalies Include: Offline Inverters and Combiners, Anomalous Strings, Tracker Off Alignment or in Stow, and Module Level Faults affecting the entire module’s performance.
Standard Level Inspection
Summary: Standard level aerial inspections balance altitude, speed, and granular site data. The level of detail in the collected data provides teams an understanding of the performance of 100% of the PV system modules.
Infrared thermal imagery: 5-6 cm/px resolution
HD RGB Imagery: 1.5-2 cm/px resolution
Identifiable Anomalies Include: All anomalies identified at the Overview level, as well as physical and visible module damage including cracked/broken modules, thin-film delamination, soiling and surface coverage of the PV module(s). Additional sub-module findings also include: diode faults, cell and multi-cell defects, and faulty junction box. Suspected PID, shading issues due to tree lines, obstructions, or adjacent rows, and damage to rows and tables.
Comprehensive Level Inspection
Summary: Comprehensive level aerial IR inspections are performed in compliance with IEC standards. It provides highly detailed, sub-module level granular data and allows teams to thoroughly understand the performance of each PV module. This inspection level offers absolute temperature accuracy and enables accurate sorting and prioritisation of both module and string-level anomalies by temperature intensity.
Infrared thermal imagery: 3 cm/px resolution
HD RGB Imagery: 1 cm/px resolution
Identifiable Anomalies Include: All anomalies identified at the Overview and Standard levels as well as data analysis in accordance with IEC TS 62446-3 Technical Specification: Photovoltaic (PV) systems. More detailed classifications of single-cell hot spot with ΔT > 10 K, heated junction box with ΔT > 4 K, and substring in short circuit with ΔT > 4 K.
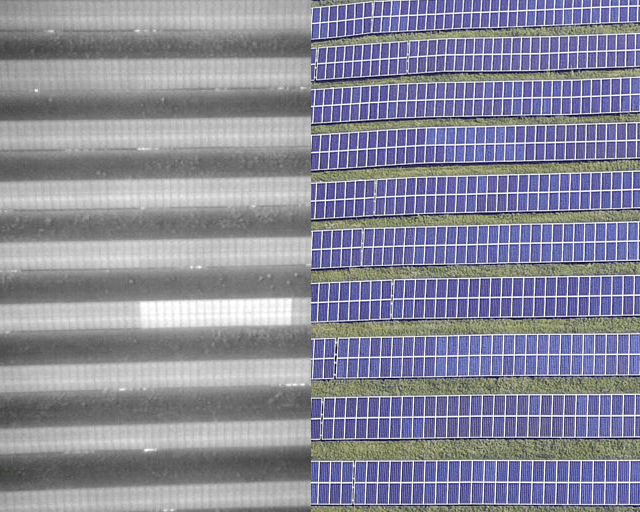
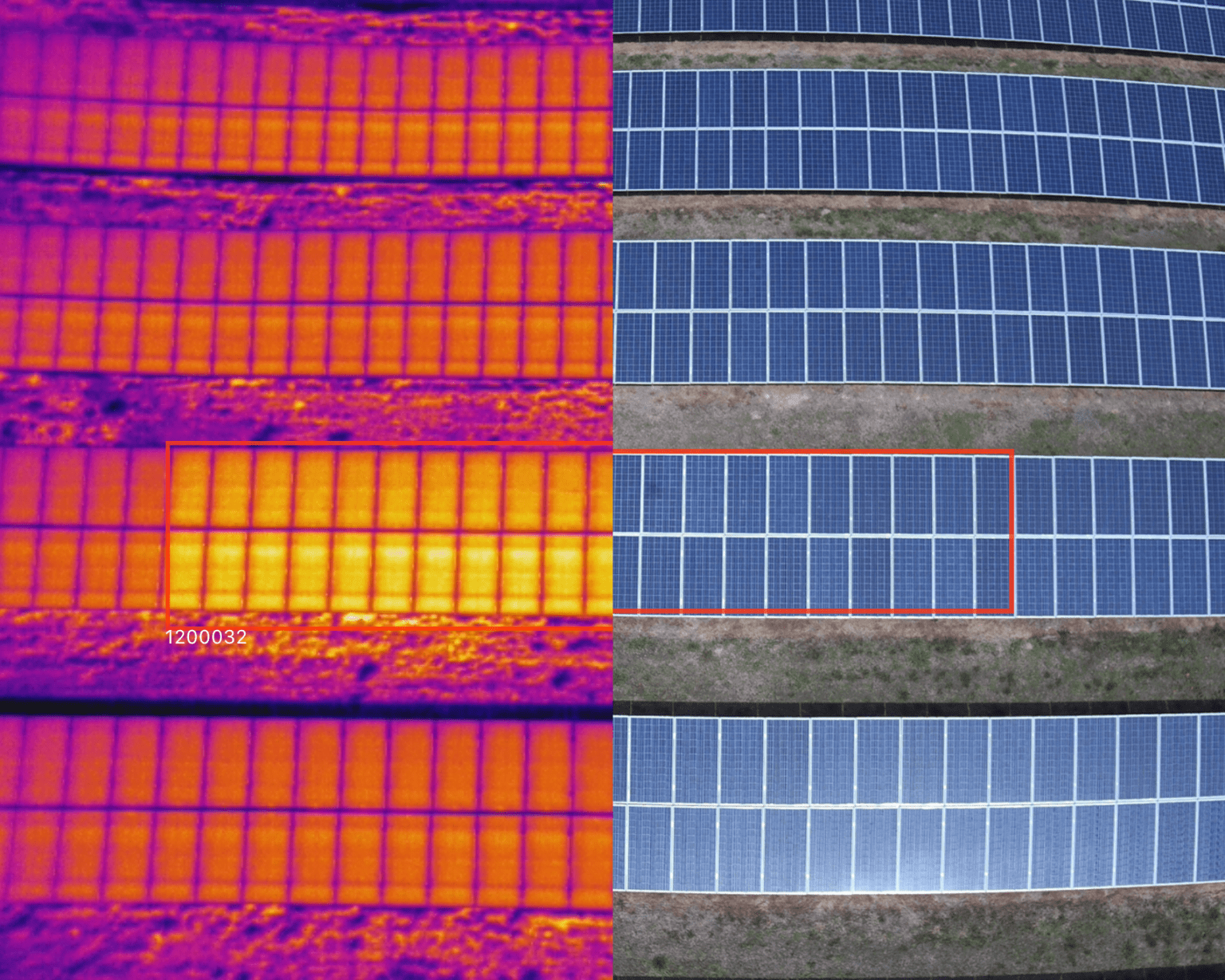
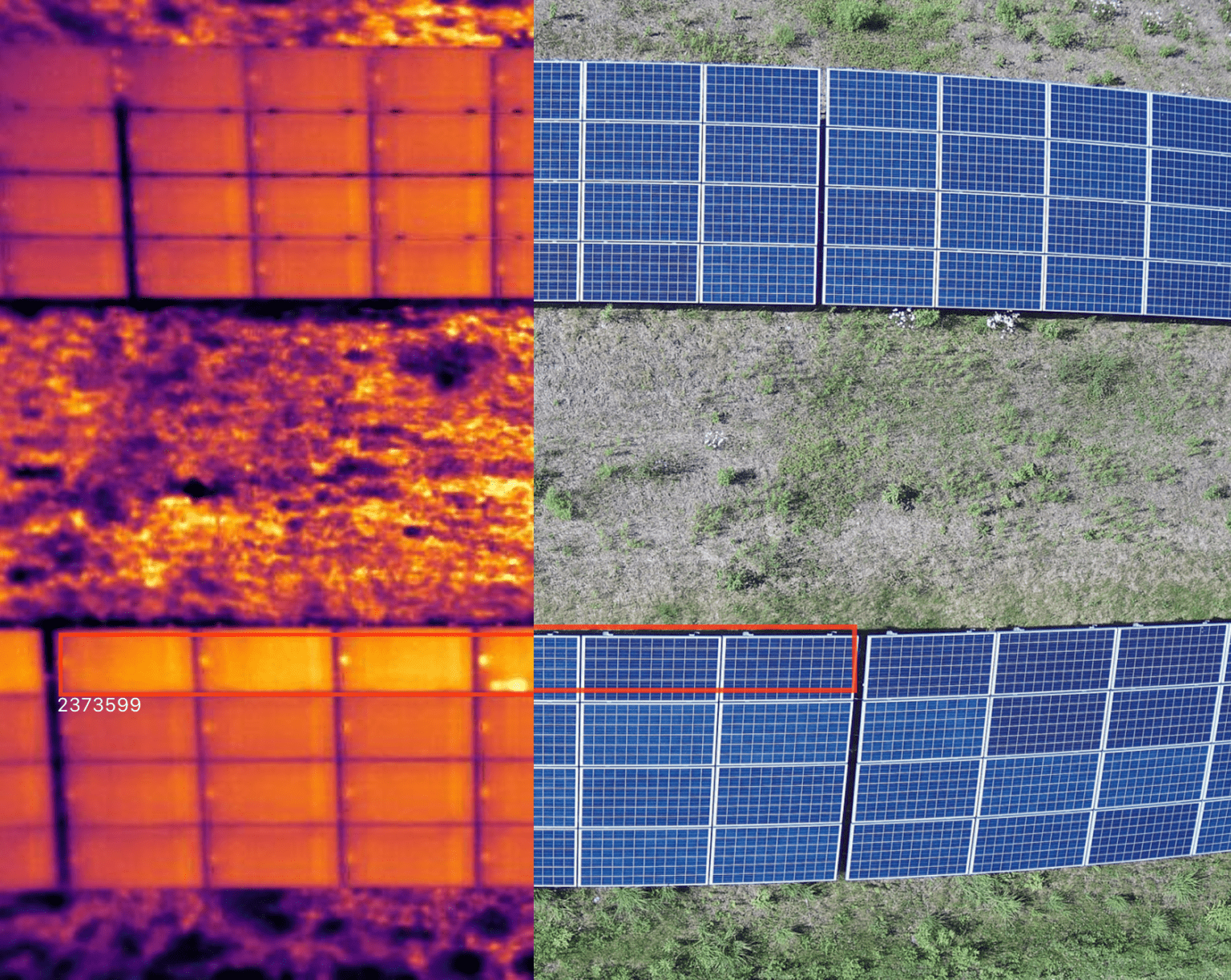
Case Study: A 500 Acre Utility Scale Solar Farm. One advantage of flying a drone versus the traditional approach of walking a ground-based surveyor is a large area can be scanned in a day versus requiring weeks to walk. This was the case for a contractor that needed to scan 500 acres at the start of a utility scale solar farm project. This contractor needed a very dense point cloud to provide the base data as the foundation for planning and design purposes.
Wind Turbine Inspection
The global installation of wind capacity is on track to reach 1000 gigawatts. In part, this growth is driven
by the expansion of turbines into punishing environments, such as sandy deserts and saltwater seas. Engineers are also pushing the limits of turbine size: GE’s Haliade-X will be the largest offshore wind turbine in the world, with blades reaching 107-meters in length.2 Combined, these trends are placing unprecedented stress on wind turbine blades.
As the scale of wind power production grows, so does the need for a means to safely and effectively maintain blades, anticipate blade failure, and keep assets generating maximum output. But existing inspection methods can be error-prone and dangerous.
UAvs provide access to hard-to-reach locations by getting right up next to the blade and taking 3-D pictures that show any signs of damage.
Visual imagery with zoom capabilities are perfect for inspections of wind turbines, or for other power infrastructure where climbing or other traditional methods of inspection are dangerous, costly and slow. Thermal sensors are perfect for uses such as inspection of solar fields, or identifying sources of heat loss in power plants. Drones are able to cover acres of solar fields quickly and efficiently with pre-planned flight modes, and are safer and more cost effective than other methods of in-flight data collection.
Wind turbines need to be routinely inspected for weaknesses and defects to maintain safe and proper function. Traditional methods of inspection are dangerous, time-consuming and expensive. Drones practically eliminate the risk, and dramatically reduce the cost and time of each inspection. Drones provide access to hard-to-reach locations by getting right up next to the blade and taking 3-D pictures that show any dents or holes.
Passive Thermography and Thermal Image Subtraction
Utilising passive thermography and thermal image subtraction techniques, internal structures and anomalies can be seen using thermal images gather by drone. This is an area that is brand new and one we’re keen to continue to develop.